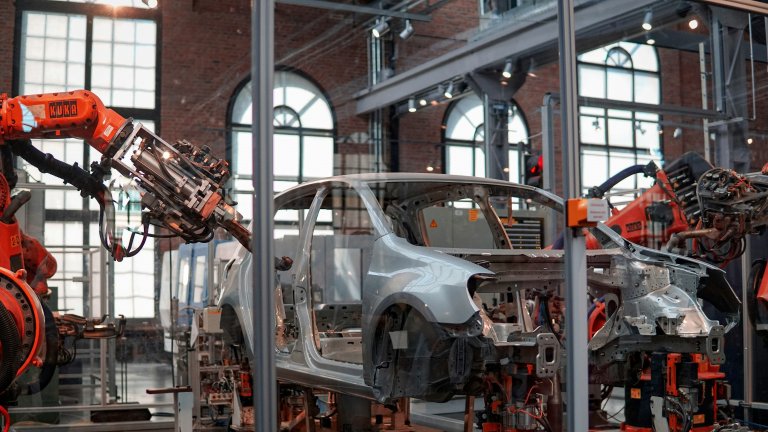
Fraunhofer-Forschende haben mit Industriepartnern einen neuen Bioverbundwerkstoff zur Herstellung von Fahrzeugunterböden entwickelt und damit die CO2-Bilanz des gesamten Produktionszyklus deutlich verbessert.
Armaturenbretter aus Sisal, Türverkleidungen aus Flachsfasern oder Sitzschäume aus Soja: In der Fahrzeugindustrie werden immer öfter erdölbasierte Materialien durch biobasierte Werkstoffe wie naturfaserverstärkte Kunststoffe ersetzt. Meist handelt es sich dabei um Verkleidungsteile, die keinen hohen mechanischen Belastungen ausgesetzt sind. Bauteile wie Fahrzeugunterböden müssen hingegen jedem Crash standhalten und bestehen daher oft aus glasfaserverstärkten Kunststoffen. Diese sogenannten Hochleistungswerkstoffe ebenfalls durch leistungsstarke biobasierte Materialien im Automobilbau zu ersetzen, das ist einem Forschungsteam nun gelungen.
Unterboden aus Naturfasern und Kunststoff-Rezyklat
Gemeinsam mit Industriepartnern entwickelten Forschende vom Fraunhofer-Institut für Holzforschung – Wilhelm-Klauditz-Institut (WKI) einen Fahrzeugunterboden, der aus Naturfasern sowie recycelten Kunststoffen besteht. Durch den Einsatz von Flachs-, Hanf- und Cellulosefasern besteht das Fahrzeugteil bis zu 45 % aus Naturfasern. Zudem wurde bei der Herstellung des Naturfaser-Kunststoff-Compounds vollständig auf neue Polymere wie Polypropylen verzichtet und es kamen ausschließlich Rezyklat zum Einsatz.
Die Entwicklung des neuen Bauteils wurde durch das Bundesministerium für Wirtschaft und Klimaschutz gefördert. Neben den Fraunhofer-Forschenden waren daran beteiligt das Thüringische Institut für Textil- und Kunststofftechnik (TITK), die Röchling Automotive SE & Co. KG, die BBP Kunststoffwerk Marbach Baier GmbH sowie die Audi AG. Für die Entwicklung der biobasierten Materialien für den Spritzguss war das WKI-Team verantwortlich. Hier kam es vor allem auf die richtige Kombination der Compounds an.
Keine Einbuße bei Steifigkeit und Festigkeit
„Naturfaser-Spritzguss-Compounds sind bisher vor allem durch Festigkeits- und Steifigkeitssteigerungen gegenüber unverstärkten Polymeren bekannt. Bei der Entwicklung im Fahrzeugunterboden ist es darüber hinaus gelungen, durch eine innovative Kombination von ausgewählten Post-Consumer-Rezyklaten (PCR) als Matrix und Naturfasern unterschiedlicher Reinheitsgrade die hohen Anforderungen an die Kaltschlagzähigkeit zu erfüllen, ohne dabei die geforderte Steifigkeit und Festigkeit einzubüßen“, erklärt Moritz Micke-Camuz, Projektleiter am Fraunhofer WKI.
Die Projektpartner am TITK und bei Röchling stellten schließlich aus dem naturfaserverstärkten Mischfaservlies erste Faserverbundbauteile (Lightweight-Reinforced-Thermoplastic, LWRT) her. Damit der Unterboden auch gegen Feuchtigkeit gewappnet ist, mussten die Flachs- und Hanffasern imprägniert werden. Hierfür entwickelte das Fraunhofer WKI ein Furfurylierungsverfahren für LWRT-Bauteile, wodurch die Feuchtigkeitsaufnahme der Fasern um bis zu 35 % reduziert wurde, ohne die Biegefestigkeit der späteren Bauteile zu beeinträchtigen.
Bio-Leichtbau-Material für Serienproduktion geeignet
Komponententests sowie Fahrversuche mit den ersten hergestellten Prototypbauteilen waren vielversprechend. Im Rahmen der Serienerprobung in der vom VW-Konzern neuen „Premium Platform Electric“ seien erfreuliche Testergebnisse erzielt worden, heißt es. Demnach erfüllten die neu entwickelten Bioverbundwerkstoffe alle technischen Anforderungen an Unterbodenbauteile und erwiesen sich als absolut serientauglich. Weder der Einsatz von Naturfasern, noch von (Post-Consumer-)Rezyklaten habe zu einer signifikanten Beeinträchtigung der Eigenschaften geführt. Den Forschenden zufolge könnten aus technischer Sicht Fahrzeugunterböden zukünftig vollständig aus dem neuen, hochleistungsfähigen Bio-Leichtbau-Material hergestellt werden.
CO₂-Emissionen um 40 % reduziert
Darüber hinaus fällt auch die CO₂-Bilanz des neuen Fahrzeugteils wesentlich günstiger aus. Durch den Einsatz von Naturfasern und Rezyklat können demnach CO₂-Emissionen während der Produktion, der Nutzung und des Produktlebens um bis zu 40 % reduziert werden, schreiben die Forschenden.