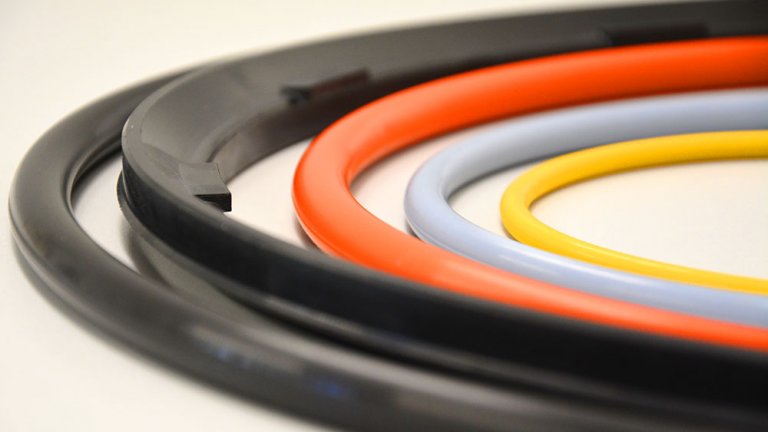
Trocknen in der Mikrowelle
Sie haben einen Durchmesser von 1,50 m und eine Schnurstärke von über 20 mm – die Riesendichtungsringe, die die traditionsreiche Kunststoff- und Gummiverarbeitung aus Motzen in alle Welt liefert. Eingesetzt werden die Jumbo-Dichtungen vor allem in Baumaschinen, Muldenkippern und riesigen Mining Trucks. Doch je größer und dicker diese Dichtungen aus hochentwickelten Elastomeren sind, desto anfälliger sind sie für innere Spannungen, die oftmals zum Platzen der Ringe führen.
„Der Werkstoff Gummi lebt“, weiß Thomas König, geschäftsführender Gesellschafter der Motzener Kunststoff- und Gummiverarbeitung GmbH, aus jahrzentelanger Berufserfahrung. Auch sein Unternehmen, das 1993 privatisiert wurde, lebt so gut wie nie zuvor. Seit 1931 eine feste Größe am Kunststoffverarbeitungs-standort Motzen beschäftigt es heute mehr als 70 Mitarbeiter im Drei-Schicht-Betrieb und fertigt neben seiner „Spezialität“ – Mehrkomponententeile – auch Gummidichtungen. Zu den Abnehmern der Formteile gehören weltweit führende Hersteller von Bau-, Abraum- und Bergwerksmaschinen.
Manche platzen auf wie Bockwürste
Gerade die großen Dichtungen für Fahrzeugachsen müssen extreme Belastungen aushalten. Denn die gewaltigen Mining Trucks laufen rund um die Uhr. Stand- und Ausfallzeiten sind teuer.
Um die Qualität zu gewährleisten, verarbeitet das Motzener Unternehmen „technisch hochgezüchtete“ Elastomere. Diese werden bisher nach dem Spritzgussprozess in einem zusätzlichen, aufwändigen Arbeitsschritt getempert. Darunter versteht man das Nachbehandeln des Materials in riesigen Bäckeröfen, damit die Gummidichtungen die nötige mechanische Festigkeit erhalten. Aber nicht bei allen Ringgrößen gelingt das: „Gerade viele der großen Teile sind uns im Temper-Ofen aufgeplatzt wie eine Bockwurst“, sagt Geschäftsführer König. Trotz Zwischenlagerung vor Versand an die Kunden wird ein Teil der Dichtungen durch die innere Spannung noch Tage später förmlich zerrissen. Eine unakzeptable Reklamationsquote von 30 Prozent – gegenüber von fast 0 Prozent bei kleinen Ringstärken – ist die Folge.
Forschungspartner PYCO entdeckt Ursache und Lösung
Mit Unterstützung durch den Kleinen und später Großen Innovationsgutschein hat Thomas König Wissenschaftler von der Fraunhofer-Einrichtung PYCO ins Boot geholt. „Wir haben über Kontakte im Cluster Kunststoffe und Chemie erfahren, dass die PYCO über Großgeräte wie einen Autoklav und eine Industriemikrowelle verfügt.“
Die PYCO-Forscher fanden heraus, dass die Großdichtungen ein Feuchtigkeitsproblem haben. Bei der Herstellung der Gummiringe wird Wasser als Spaltprodukt freigesetzt und in das Material eingelagert. Außerdem befindet sich Restfeuchte im Werkstoff. Spaltprodukt und Restfeuchte lassen die Ringe während des Temperns zerbrechen.
Die laufenden Untersuchungen im Rahmen des Großen Innovationsgutscheins setzen diese Erkenntnisse fort und beleuchten eine Lösung – die Mikrowellentechnologie. Durch sie wird das Material von innen nach außen getrocknet und getempert, sodass die Restfeuchte entweicht, die Ringe stabil werden und die Vulkanisation abgeschlossen wird. Bis Ende 2014 liegen die endgültigen Ergebnisse vor.
Dann wird die Motzener Kunststoff- und Gummiverarbeitung GmbH kräftig in die Mikrowellentechnik investieren. „Dies würde uns ein Alleinstellungsmerkmal verschaffen. Und so den sowohl zukunftsträchtigen wie einträglichen Markt für große Nutzfahrzeug-Dichtungen öffnen helfen.“