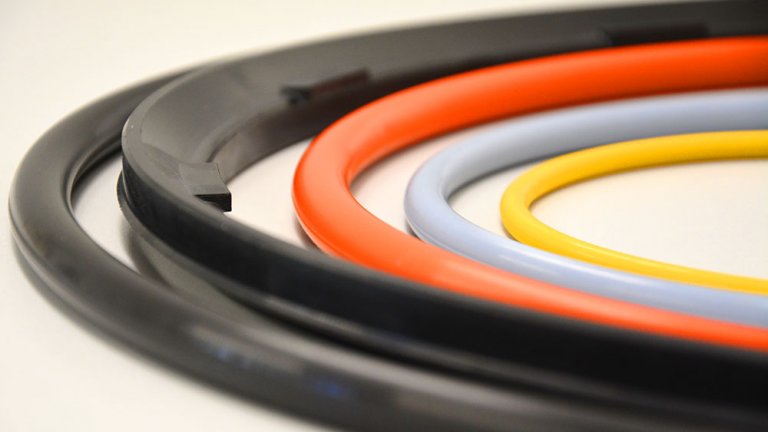
Drying in a Microwave
The giant O-rings produced by a long-standing plastics and rubber processing company from Motzen with a diameter of 1.5 m and a cord thickness of over 20 mm are being shipped to all corners of the world. The oversized O-rings are being used predominantly for construction machinery, mining vehicles and giant mining trucks. However, with the growing size and thickness of these O-rings, which are being produced from sophisticated elastomers, internal stress might grow as well and often it can even make the rings burst.
“Rubber as a raw material is well and alive,” knows Thomas König, Managing Partner at the company Motzener Kunststoff- und Gummiverarbeitung GmbH, from decades of professional experience. The company was privatised in 1993 and it is better off than ever before. Since 1931 the company has been a stable and important part of the plastics processing location Motzen. Today more than 70 employees work a three-shift schedule. Besides its “speciality” – multi component parts – it also produces rubber seals (O-rings). Among the buyers of the moulded parts are globally leading producers of construction machinery and mining-specific machinery.
Some burst like the famous German bockwurst
Especially the large seals for vehicle axles have to withstand extreme strains as the huge mining trucks are in use around the clock. Downtimes and idle times are expensive.
In order to be able to reach the desired quality, the company from Motzen processes “technologically cultivated” elastomers. Up until now these elastomers had to first go through an injection moulding process and then through an additional and demanding tempering work stage, which means that the material had to undergo a post-treatment in giant stoves. This work stage gives the rubber seals the necessary mechanical resistance. However, this does not work for O-rings of all sizes: “It was mainly the larger ones that burst like German bockwursts in the tempering oven,” says Managing Partner König.
Despite being put in temporary storages prior to their shipment to the customers, a part of the seals practically burst open due to inner strains even days after being finalised. An unacceptable complaint rate of 30% resulted from this phenomenon, which is especially striking in comparison to the almost 0% in the case of smaller O-rings.
Research partner PYCO discovers the cause and comes up with a solution
First the company received the Small Innovation Voucher and later the Grand Innovation Voucher. This support enabled Mr König to bring scientists from the Fraunhofer research institute PYCO on board. “Our contacts within the Cluster Plastics and Chemistry informed us that the research institute PYCO owned large-scale equipment, for example an autoclave and an industrial microwave.”
The researchers at PYCO found out that the very large seals suffered from a humidity-based problem. During the production of the rubber rings, water is being released as a fission product and it embeds itself in the material. Additionally, there is a residual humidity in the raw material. The fission product and the residual humidity make the rings burst during the tempering.
The ongoing studies through the Grand Innovation Voucher are building on these findings and investigating potential solutions, which might be found in the field of microwave technology. This technology dries and tempers the material from the inside to the outside, which lets the residual humidity escape, stabilises the rings and finishes the vulcanisation process. The final findings will be available by the end of 2014.
Subsequently, the company Motzener Kunststoff- und Gummiverarbeitung will make considerable investments into microwave technology. “This would give us a unique feature and, at the same time, it would help us access the promising and lucrative market for large commercial vehicle seals.”