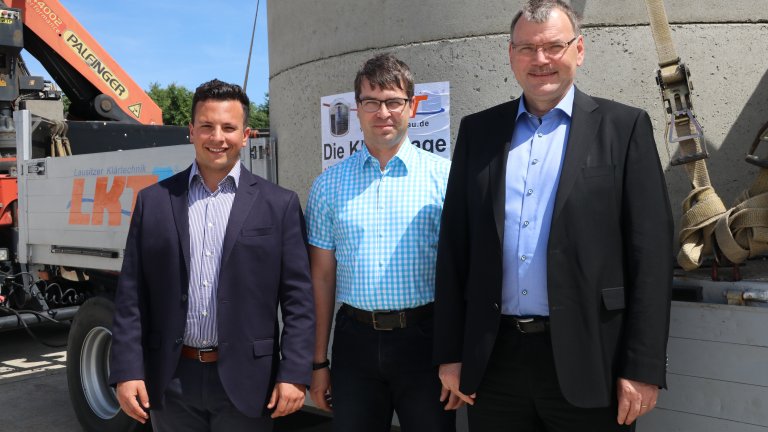
Innovation in the Underground
This project from Lusatia could revolutionise the renovation of pump shafts. Gone are the days of restoring old concrete shafts damaged by corrosion by applying a new inner layer of mortar, by bolting on plates in order to cover up the damage, or by inserting a narrower concrete tube. “We didn’t want all of that,” says Michael Müller, Manager of the company Lausitzer Klärtechnik GmbH in Luckau.
Together with scientists of the Brandenburg University of Technology Cottbus-Senftenberg, the folks from Lusatia developed a completely new system for repairing dilapidated shafts of pumping systems. “We are working with fibre-plastics composites,” points out Marcello Ambrosio of the department Lightweight Design with Structured Materials of the Brandenburg University of Technology, which is headed by Prof. Holger Seidlitz. The system consists of a layer comprised of textiles and glass fibres with a thickness of almost 1 cm that is very light and flexible, and it only acquires its extreme solidity when liquid resin, which then cures, is added.
Marcello Ambrosio explains how this light material can repair and support heavy shafts: first of all a 3D scanner is lowered into the shaft in order to carry out measurements; the data is then used for the cutting of the textile strips and the glass fibre material, which is supposed to serve as the lining of the entire shaft; a pressure bag is then used to press the flexible material from the centre of the shaft to its wall; only then is the material infused in liquid resin. Through the curing of the resin the concrete shaft receives something that resembles a “girdle” and that sticks to its wall, covers up damaged areas and even stabilises the shaft. Then the pressure bag is removed.
The renovation can be performed much quicker in comparison to conventional renovation methods
“The whole process takes only as long as two hours,” says the Manager of LKT, Michael Müller. In order to repair a shaft, it has to be pumped dry, which means that it is out of order. Conventional renovation methods lead to downtimes of up to 2 weeks. The company LKT wants to reduce this time span to 2 days. “This reduces costs,” points out Torsten Hansen of the company’s Technical Department. The company LKT GmbH produces and distributes small sewage treatment systems and pump stations worldwide. The company’s about 60 employees also conduct the maintenance work on the systems, which means that the next step towards the renovation of shaft systems was a rather small one.
Once placed in the shaft, the protecting layer later on serves as a leakage detector
The company’s innovation has another huge advantage: it also works at low temperatures. Very thin heating wires are worked into the material and maintain the temperature of the resin at a certain level in order for it to remain fluid during the process. The wires stay in the material and later on they function as leakage detectors. In the event of new damage to the shaft causing water to leak out of the shaft or, inversely, substances to enter into the shaft, the humidity changes the resistance of the heating wires. This information is then forwarded directly to the operator of the system. The process will enter the phase of test runs in autumn. A corresponding patent has already been filed. The company LKT intends to bring it to the market in 2018. LKT has already received many requests. Michael Müller wants to push the development even further so that products from his plant will be coated with the new material right away; in comparison to conventional coatings this happens in a cost neutral way. The research project “FlexRehaSchacht” with the Brandenburg University of Technology will continue until the end of 2018.